Thursday, 18 August
9am: We reconvened at the test-beam area. First thing on the agenda was a second visit from the safety service, who wanted to see if we could improve on the grounding of our system – to protect people from any possible chance of electrocution. The risk was already extremely low (and, in any case, people are not permitted near the equipment when it is running) but we still managed to improve things a bit.
Grounding and shielding of devices under test isn’t just for safety, but also to reduce “noise” entering the system and ruining our signals. So we also spent some time attaching grounding wires to various places in an effort to minimise the noise. Mobile phones are invaluable for this sort of thing, with one person (in the beam area) modifying the grounding and the other person (in the control room) running the software to measure the noise. After about a dozen variants we found one that minimized the noise. Sometimes cutting-edge science involves some trial and error!
Now we were ready to try to “see” some particles in our detector. This isn’t as easy as it may sound. The particles are traveling close to the speed of light and the signal from the detector is very fast – less than a millionth of a second! We need to know when to look in our detector for this signal. So we have other well-understood detectors also in the beam that, together with some electronics, produce a “trigger” signal – to tell us when to look.
In the diagram above, the “trigger scintillator” represents a special piece of plastic that produces a small flash of light when a particle passes through it. The light is converted to an electrical signal that is passed to the “trigger electronics”. Finally, the trigger signal is sent to the device being tested – in our case a hexagonal silicon sensor about 15cm across. But all that takes time – perhaps a couple of hundred billionths of a second. Which doesn’t sound like much! However, the particle passes through our sensor about 3 billionths of a second (3 ns) after it went through the scintillator. So, by the time the trigger signal arrives at the sensor, the particle would have long since departed! The sensor electronics thus need an onboard memory, to store data for a short amount of time. If it receives the trigger signal during this time, the data are sent to the outside world. If not, the data are erased. This is what is done in practice. However, it is not as simple as that, as the synchronisation between the trigger signal and the data stored in the sensor electronics needs to be precise. This is another case of trial and error, adjusting cable lengths to adjust the synchronisation. And these adjustments can take a long time – hours or days – as we are talking about synchronisation to the level of billionths of a second. Better than any Swiss watch!
12pm: It all came as a bit of a shock when, at the first attempt to take data, we actually saw signs of signals in our device! My jaw dropped to the floor as my colleague Rajdeep simply said, “Yeah, we have some nice signals here.” To be fair, he had been very confident that we would see something quickly, having been involved in previous tests at Fermilab where a majority of the debugging took place. But still, to have a positive result so quickly was fantastic.
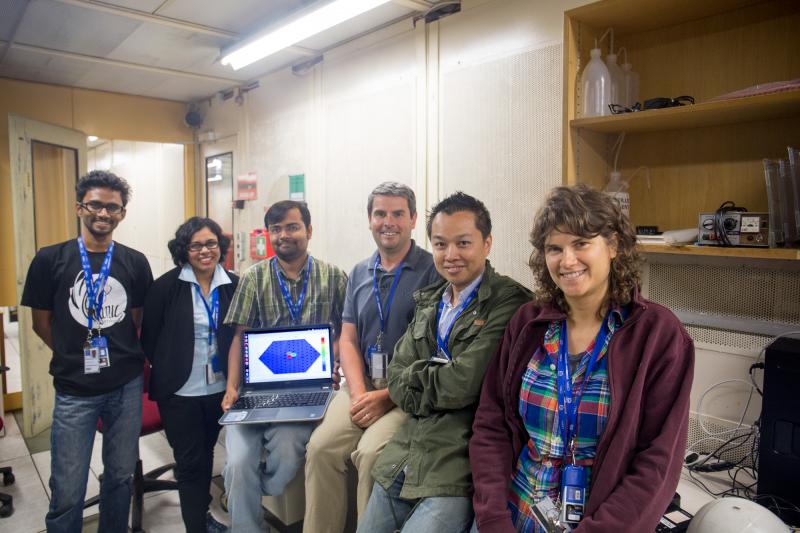
2pm: Despite the euphoria in the morning, there was still a lot to do. The size of the signals we saw was not perfect – indeed it was much lower than we expected. This meant we were not perfectly synchronised. So we started to add extra cables into our system to delay the trigger by some tens of nanoseconds, hoping the signal would increase as we improved the synchronisation. Unfortunately the signal decreased, meaning that we were just getting worse by adding more cables. And removing cables is not an easy thing to do! But we did manage to reduce some cable lengths, resulting in an overall gain of about 30 billionths of a second. This did make some improvement, but not enough.
It looked like we needed to gain another 500–600 billionths of a second! This was just too much – there had to be something wrong with our system…
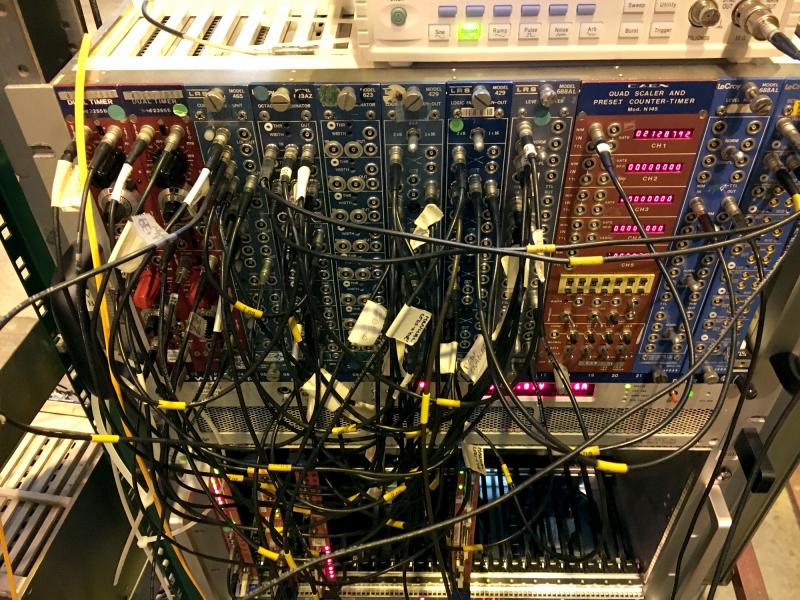
4pm: While all this was going on, I had another “fun” job to do: to prepare a shift list. As beam time is precious, we want to take a lot of data and that meant having people in the control room most of the time. As we only have a small system on this occasion we chose to have just two shifts: 8am→4pm and 4pm→midnight. Each shift has to have at least two people (for safety purposes). And we have a lot of shifts to cover! Fortunately I had a team of 14 people to take shifts, plus a few “experts” who would be available 24/7 at the other end of a phone call. And although the process of making the shift list is tedious and complex (with many constraints), it is a pleasure to have such an international team of people to work with. The nationalities of the people involved in this small test are: German, Italian, Indian, Chinese, Taiwanese, Turkish, French, Russian and British. All of whom speak excellent English as well as their mother tongue, and often in addition to one or more other languages! It puts me to shame with just English and some French (and my French accent needs, ahem, “work”, let’s say).
9pm: After a lot of fighting with trying to improve the synchronisation we decided to call it a day and try to do some accurate measurements the next day, to see if we could understand our problems better. We asked some of the sheep – residents of the Prévessin site – to help us, but they didn’t seem to care.
Friday, 20 August
9:30am: We needed to measure the time the electronics were taking to make the trigger decision. A colleague from Caltech (Adi) brought a great gadget (see https://www.psi.ch/drs/drs-chip) based on a chip called the DRS, developed at one of our collaborating institutes – the Paul Scherrer Institute (PSI) in Switzerland. It is similar to an oscilloscope but uses a laptop computer as the screen and control interface. We connected the output of the scintillator to one channel of the DRS and the output of the trigger electronics to another channel. What we saw on the screen surprised us a lot! The trigger signal came about 180 billionths of a second after the scintillator signal – which was OK. But the trigger signal was a negative pulse followed by a positive pulse about 600 billionths of a second later – exactly the opposite from what we wanted and expected to see.
And as our device only sees the positive part of the trigger signal it was clear that we needed to invert the trigger signal. This was rather easy to do, simply using a different output from our electronics. In another case of serendipity, the inverted output worked and increased our signal by more than a factor of 3 – a sure sign that we were now close to the optimum time. It was now 1:40pm – time to rush to the CERN cafeteria before it closed!
2:30pm: Tutorial time! Most of the volunteers and experts came to the beam area for an introduction to the beam-/access-control system, the data-acquisition system and the analysis tools. These latter are a critical part of operation: we need fast feedback to ensure that the data we take are good.
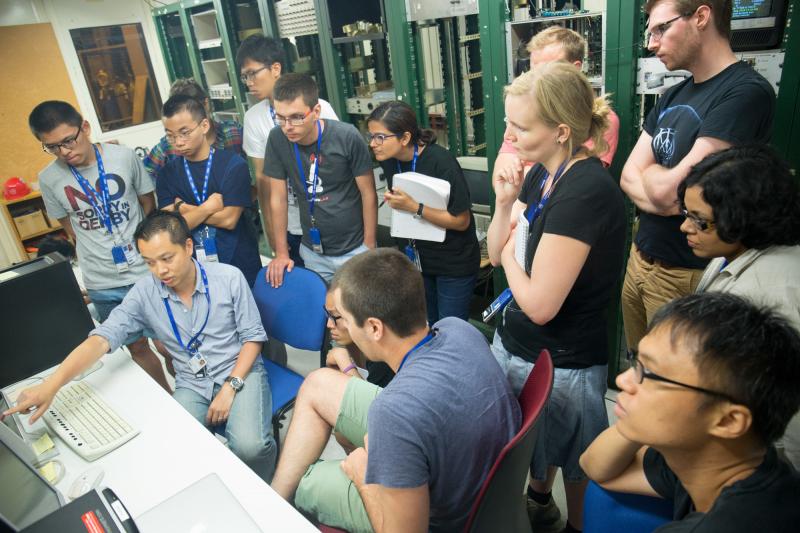
5pm: Our first two “shifters” started taking data, according to a plan that had been devised to make the most of our beam time. We spent a couple of hours optimising the timing further and we were then ready to start taking data. Well, almost. We saw that the beam particles were hitting our sensor just a little above its centre. We asked for access to the beam area – which is a very tightly controlled zone – and moved the support table up a little, to centre the beam.
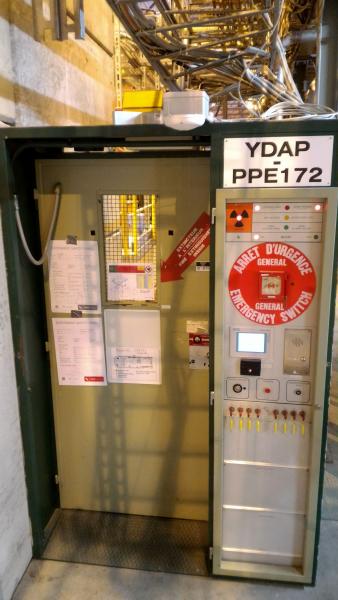
Then came one of those moments when the world goes into slow motion and you can’t do anything about it! Just as we were exiting the area, I saw one of my colleagues go to press the wrong button to exit: the emergency button instead of the normal exit button. My shout of “Nooooooooo” seemed to last for ages but to no avail: the button had been pressed. The zone was now completely shut down and no longer under our control. Fortunately the CERN Control Centre is a short drive away, so I got a “reset key”, did a safety check and closed the zone. We took some data to see if our movement of the table made a difference: it did. We were finally ready.
We began with 150 GeV electrons incident on a 5cm-thick lead brick placed just before our sensor. The electrons interact with the lead and produce a “shower” of particles that pass through our sensor. The higher the incident electron’s energy, the more particles in the shower and the bigger the signal in our sensor. This is the principle of a calorimeter – a particle detector to measure particle energy.
The rest of the evening went rather smoothly, taking a lot of data with 150 GeV electrons and some with 20 GeV electrons. At midnight we changed the beam type to pions, removed the lead brick and started a long overnight run. This was to explore the sensitivity of our sensor to single particles rather than the hundreds in the showers. We would see the results in the morning.
- Previous entry in "Test-beam tales": Day 1
- Next entries in "Test-beam tales": Days 4 and 5, Days 6 and 7
The views expressed in CMS blogs are personal views of the author and do not necessarily represent official views of the CMS collaboration.